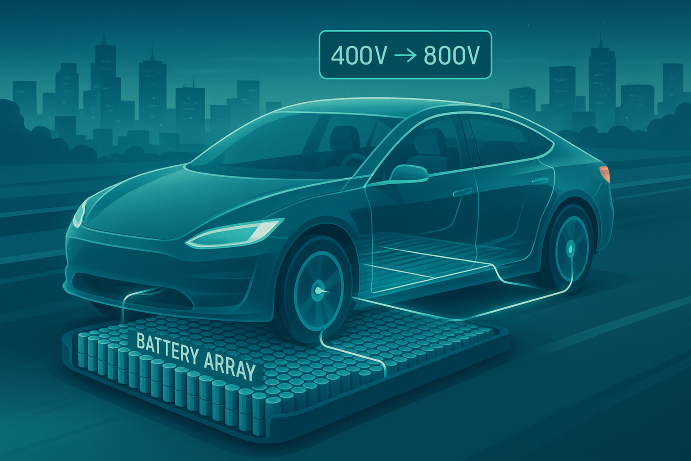
Tech Innovations Help Consumers Say Goodbye to EV Range Anxiety
Financial incentives and future legislation are pushing EV adoption, but advanced power electronics and battery technologies are crucial to addressing range anxiety and driving broader acceptance.Range anxiety, the feeling of concern over the distance an electric vehicle (EV) can travel on a charge, is typically cited as the primary reason that EVs continue to see modest adoption. While both the carrot, in the form of financial incentives, and the stick, in the form of future legislation banning internal combustion engine (ICE) vehicles from entering major cities, are being employed to incentivize consumer adoption of EVs, extending the range of EVs is one of the most important factors to address to drive broader adoption.
One theme that I have highlighted in every blog to date is that the automobile has significantly transformed from the historical adoption of trailing-edge electronic technologies. Today’s vehicles and those on the drawing table (or maybe now it’s in the CAD tool) push the boundaries of employing state-of-the art technologies. Power electronics, specifically those used to power the electric motors of the EV and the associated control electronics and architectures, are no exception.
In this blog, I’ll provide a very high-level overview of some of the advanced technologies and architectures associated with powering the EV drive train and where these are being pushed to further extend the range of EVs. Each of these topics could easily warrant its own blog. Suffice to say, this will be a light treatment of these topics.
A very simplified block diagram of the powertrain of an EV is shown below.
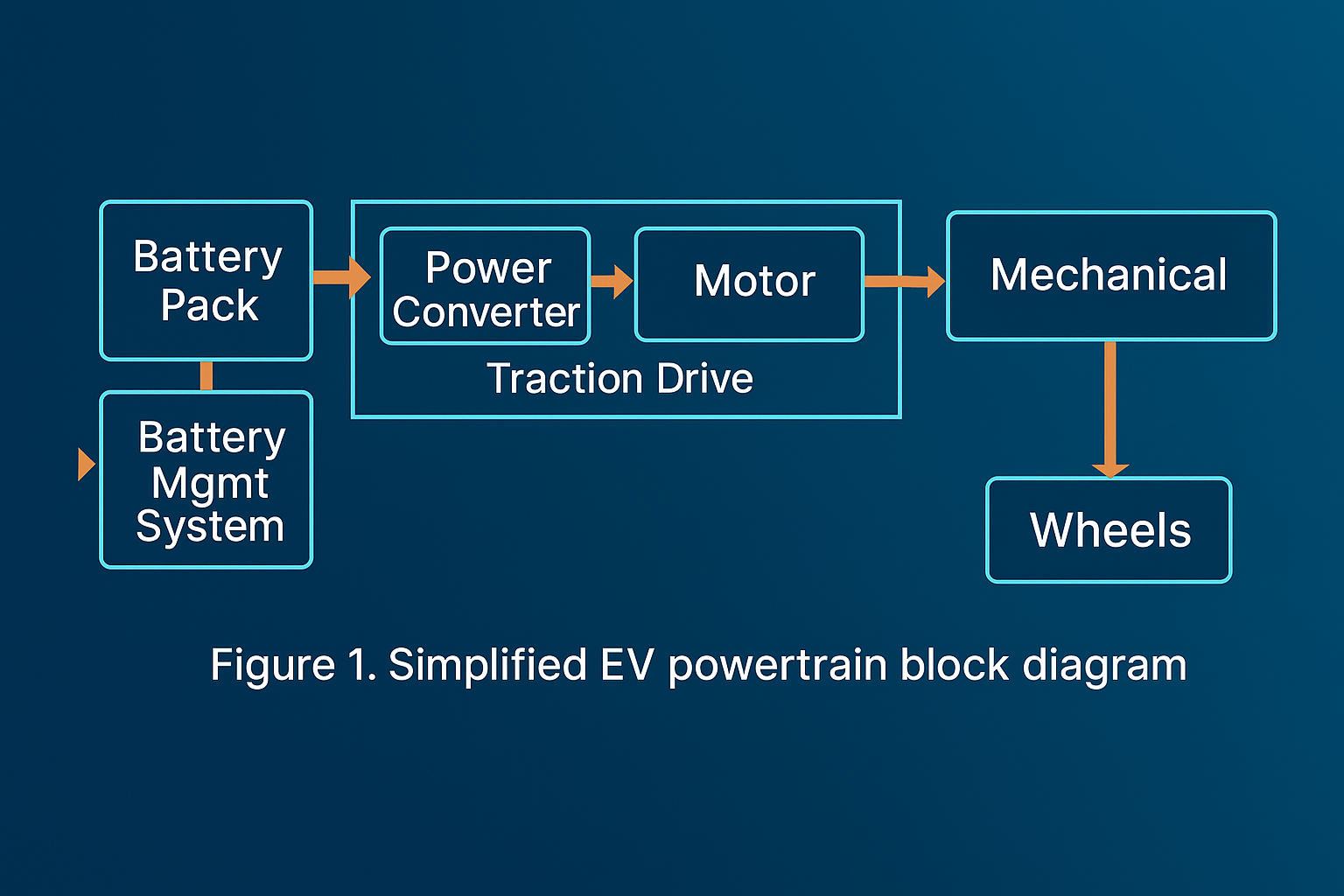
While this block diagram hardly does justice to the complexity of the EV powertrain, it provides an adequate framework to highlight some of the major building blocks and the key technologies that are employed in the EV powertrain, the impact they have on the range of the EV, and the innovations that we can expect to see on the horizon to further extend that range.
Starting with the battery pack, a typical EV on the market today consists of a total of 7,104 rechargeable 3-volt lithium-ion batteries — each roughly the size of an AA battery! These batteries are connected in series and parallel combinations to generate about 400 direct current (DC) volts (at 90 kilowatt-hours), which is used as the power source for the traction inverter. 90 kWh means that the battery pack can supply 90 kW of power for 1 hour, which is a lot of power! The average US household uses roughly 30 kWh of power in a day.
To further improve power efficiency in the future, the industry trend is for the battery pack voltage to move from 400V to 800V. That shift will lead to significant benefits in actual power consumption (reduced by a factor of 2!), which in turn leads to less heat and hence less weight required to address system-level cooling and less weight due to lighter cabling requirements. The move to 800V does, however, require the charging infrastructure and the traction inverter to support these higher voltages.
The traction inverter is responsible for supplying power to the brushless DC motors, as controlled by the accelerator. Historically traction inverters employed relatively mature power semiconductors called IGBT (insulated gate bipolar transistors). Semiconductors are typically challenged to operate at such high power and voltages, especially if high speed switching is required. While IGBTs can address the high-power demands, they offer relatively low switching performance and are not practical in the most efficient traction inverters, which are typically based on switched topologies.
Recent advances in manufacturing processes have made a relatively new class of power electronics, wide bandgap semiconductors, viable for volume production applications. Wide bandgap semiconductors can operate at very high voltage levels, power levels, and at high switching frequencies with very low resistance (no energy lost in the device). There are two different types of wide bandgap technologies — one based on silicon carbide (SiC) and another on gallium nitride (GaN). SiC can operate at higher power levels but at slightly lower switching frequencies compared to GaN, which supports higher switching frequencies at lower power levels. Both technologies offer significant improvements over the traditional IGBT devices.
Wide bandgap devices are one of the fastest growing segments in the power electronics market, driven by EVs, the EV charging infrastructure, renewable energy, and a host of other applications requiring high-power, high-efficiency semiconductors. They demonstrate how automotive now drives demand for leading-edge technologies. The ability to operate at 400V and then support the shift to 800V is only made practical through the advent and use of wide bandgap semiconductors.
The traction inverter also employs some of the industry’s leading-edge motor control techniques, which include space vector modulation (SVM) and field-oriented control (FOC) to deliver maximum inverter performance, efficiency and control over the state-of-the-art brushless DC motors. The switching circuitry topologies employed in the traction inverter also represent some of the most advanced topologies, which again focus on achieving the highest energy efficiency when driving the EV motor. With the objective to address range anxiety, there is no stone left unturned in employing innovative technologies whenever it is applicable, viable and beneficial.
The last building block in the discussion of the EV power train is that of the battery management system (BMS). The BMS also profoundly affects the range of the vehicle. As previously mentioned, the battery pack of an EV is based on thousands of rechargeable batteries that are connected in various series and parallel combinations to generate 400 volts. One of the key challenges that the BMS addresses is that each of those batteries has a different charge and discharge rate, and those rates need to be monitored and controlled to ensure batteries are not under-charged or overcharged. Under-charging will directly affect range (not a full charge), whereas overcharging can lead to catastrophic results, including fires and explosions.
The BMS uses advanced charging algorithms to ensure the maximal charge is achieved on a battery-by-battery basis, while optimizing for minimal time to achieve full charge, and without overcharging a battery or overheating the battery pack. Again, this is a non-trivial problem to solve that also leverages state-of-the art technologies, including wireless connectivity to communicate charge status to electronic control units (ECUs) that monitor the overall charging of the battery pack. Not only are advanced charging algorithms employed, but also AI is employed for preventative maintenance, flagging when a battery or battery pack is starting to fail. Over the air (OTA) update technology is also employed as new, more advanced algorithms are identified that lead to more effective charging or faster charging times.
Lastly, while not shown in the simplified block diagram, there are also significant considerations given to the vehicle architecture as it applies to the distribution of power. Similar to changes in automotive E/E architecture supporting advanced driver assistance and in-vehicle infotainment systems, trends are occurring in the power architecture of the EV in the interest of power efficiency and robustness. In a nutshell, the industry is moving from a functional architecture — where power is delivered over long cables from the power source to the EV motor, to an architecture that is based on spatial positioning, where the shortest reach can be achieved from the traction inverter to the EV motor. Each approach has its benefits and complications, but given the importance of range anxiety, expect the spatial positioning architecture to win out.
In summary, while 50 years ago the average vehicle used few electronics, just a quick look at the EV power train demonstrates the complexity of the technologies that are being employed today, and where this application area is headed. In the past, computers were considered the driver of electronics technologies, then it was computer networking, and then cellular technologies/smart phones. Today, the electronics industry acknowledges that automotive is now driving leading-edge technologies across many fronts. We live in amazing times.
Financial incentives and future legislation are pushing EV adoption, but advanced power electronics and battery technologies are crucial to addressing range anxiety and driving broader acceptance.Range anxiety, the feeling of concern over the distance an electric vehicle (EV) can travel on a charge, is typically cited as the primary reason that EVs continue to see modest adoption. While both the carrot, in the form of financial incentives, and the stick, in the form of future legislation banning internal combustion engine (ICE) vehicles from entering major cities, are being employed to incentivize consumer adoption of EVs, extending the range of EVs is one of the most important factors to address to drive broader adoption.
One theme that I have highlighted in every blog to date is that the automobile has significantly transformed from the historical adoption of trailing-edge electronic technologies. Today’s vehicles and those on the drawing table (or maybe now it’s in the CAD tool) push the boundaries of employing state-of-the art technologies. Power electronics, specifically those used to power the electric motors of the EV and the associated control electronics and architectures, are no exception.
In this blog, I’ll provide a very high-level overview of some of the advanced technologies and architectures associated with powering the EV drive train and where these are being pushed to further extend the range of EVs. Each of these topics could easily warrant its own blog. Suffice to say, this will be a light treatment of these topics.
A very simplified block diagram of the powertrain of an EV is shown below.
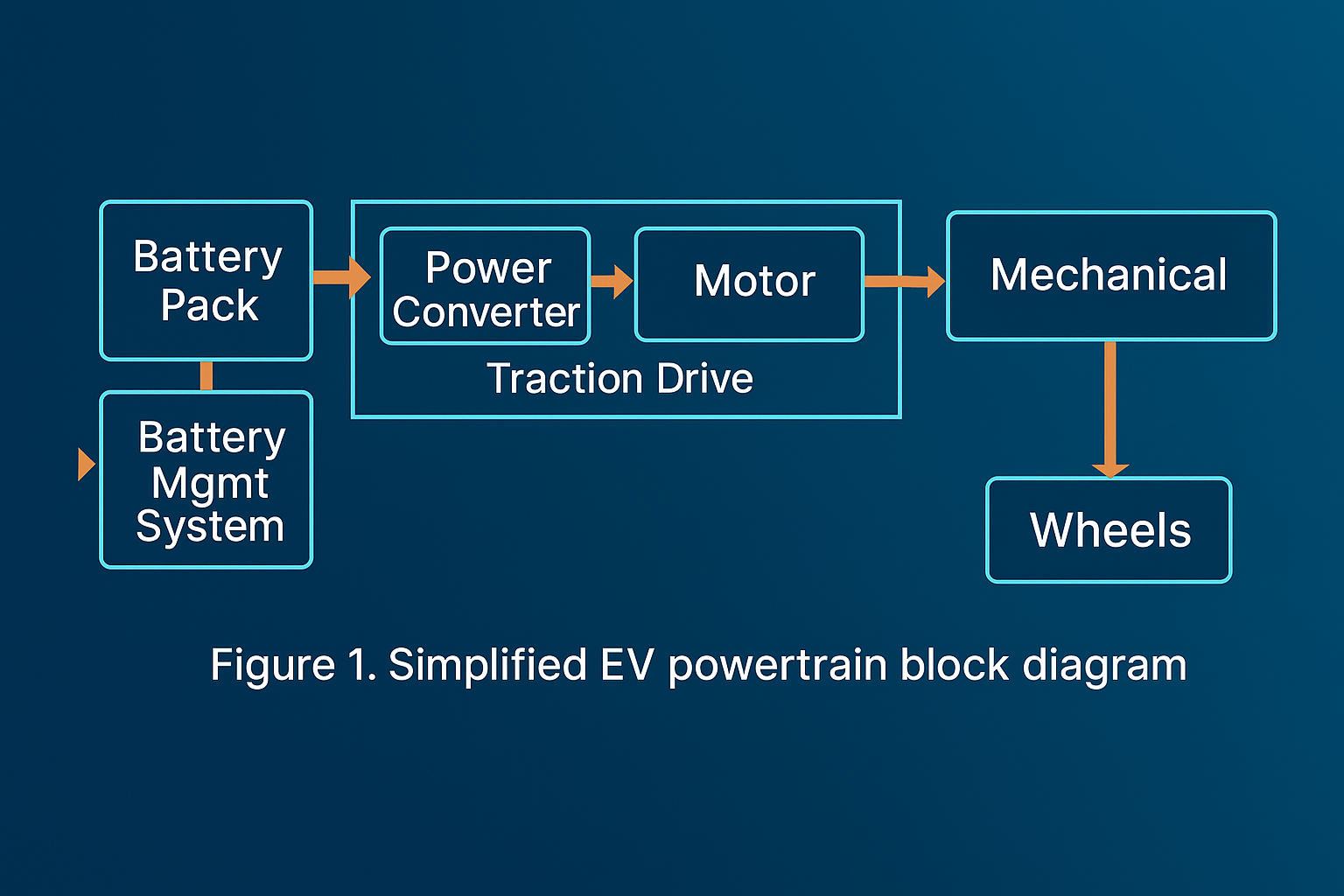
While this block diagram hardly does justice to the complexity of the EV powertrain, it provides an adequate framework to highlight some of the major building blocks and the key technologies that are employed in the EV powertrain, the impact they have on the range of the EV, and the innovations that we can expect to see on the horizon to further extend that range.
Starting with the battery pack, a typical EV on the market today consists of a total of 7,104 rechargeable 3-volt lithium-ion batteries — each roughly the size of an AA battery! These batteries are connected in series and parallel combinations to generate about 400 direct current (DC) volts (at 90 kilowatt-hours), which is used as the power source for the traction inverter. 90 kWh means that the battery pack can supply 90 kW of power for 1 hour, which is a lot of power! The average US household uses roughly 30 kWh of power in a day.
To further improve power efficiency in the future, the industry trend is for the battery pack voltage to move from 400V to 800V. That shift will lead to significant benefits in actual power consumption (reduced by a factor of 2!), which in turn leads to less heat and hence less weight required to address system-level cooling and less weight due to lighter cabling requirements. The move to 800V does, however, require the charging infrastructure and the traction inverter to support these higher voltages.
The traction inverter is responsible for supplying power to the brushless DC motors, as controlled by the accelerator. Historically traction inverters employed relatively mature power semiconductors called IGBT (insulated gate bipolar transistors). Semiconductors are typically challenged to operate at such high power and voltages, especially if high speed switching is required. While IGBTs can address the high-power demands, they offer relatively low switching performance and are not practical in the most efficient traction inverters, which are typically based on switched topologies.
Recent advances in manufacturing processes have made a relatively new class of power electronics, wide bandgap semiconductors, viable for volume production applications. Wide bandgap semiconductors can operate at very high voltage levels, power levels, and at high switching frequencies with very low resistance (no energy lost in the device). There are two different types of wide bandgap technologies — one based on silicon carbide (SiC) and another on gallium nitride (GaN). SiC can operate at higher power levels but at slightly lower switching frequencies compared to GaN, which supports higher switching frequencies at lower power levels. Both technologies offer significant improvements over the traditional IGBT devices.
Wide bandgap devices are one of the fastest growing segments in the power electronics market, driven by EVs, the EV charging infrastructure, renewable energy, and a host of other applications requiring high-power, high-efficiency semiconductors. They demonstrate how automotive now drives demand for leading-edge technologies. The ability to operate at 400V and then support the shift to 800V is only made practical through the advent and use of wide bandgap semiconductors.
The traction inverter also employs some of the industry’s leading-edge motor control techniques, which include space vector modulation (SVM) and field-oriented control (FOC) to deliver maximum inverter performance, efficiency and control over the state-of-the-art brushless DC motors. The switching circuitry topologies employed in the traction inverter also represent some of the most advanced topologies, which again focus on achieving the highest energy efficiency when driving the EV motor. With the objective to address range anxiety, there is no stone left unturned in employing innovative technologies whenever it is applicable, viable and beneficial.
The last building block in the discussion of the EV power train is that of the battery management system (BMS). The BMS also profoundly affects the range of the vehicle. As previously mentioned, the battery pack of an EV is based on thousands of rechargeable batteries that are connected in various series and parallel combinations to generate 400 volts. One of the key challenges that the BMS addresses is that each of those batteries has a different charge and discharge rate, and those rates need to be monitored and controlled to ensure batteries are not under-charged or overcharged. Under-charging will directly affect range (not a full charge), whereas overcharging can lead to catastrophic results, including fires and explosions.
The BMS uses advanced charging algorithms to ensure the maximal charge is achieved on a battery-by-battery basis, while optimizing for minimal time to achieve full charge, and without overcharging a battery or overheating the battery pack. Again, this is a non-trivial problem to solve that also leverages state-of-the art technologies, including wireless connectivity to communicate charge status to electronic control units (ECUs) that monitor the overall charging of the battery pack. Not only are advanced charging algorithms employed, but also AI is employed for preventative maintenance, flagging when a battery or battery pack is starting to fail. Over the air (OTA) update technology is also employed as new, more advanced algorithms are identified that lead to more effective charging or faster charging times.
Lastly, while not shown in the simplified block diagram, there are also significant considerations given to the vehicle architecture as it applies to the distribution of power. Similar to changes in automotive E/E architecture supporting advanced driver assistance and in-vehicle infotainment systems, trends are occurring in the power architecture of the EV in the interest of power efficiency and robustness. In a nutshell, the industry is moving from a functional architecture — where power is delivered over long cables from the power source to the EV motor, to an architecture that is based on spatial positioning, where the shortest reach can be achieved from the traction inverter to the EV motor. Each approach has its benefits and complications, but given the importance of range anxiety, expect the spatial positioning architecture to win out.
In summary, while 50 years ago the average vehicle used few electronics, just a quick look at the EV power train demonstrates the complexity of the technologies that are being employed today, and where this application area is headed. In the past, computers were considered the driver of electronics technologies, then it was computer networking, and then cellular technologies/smart phones. Today, the electronics industry acknowledges that automotive is now driving leading-edge technologies across many fronts. We live in amazing times.