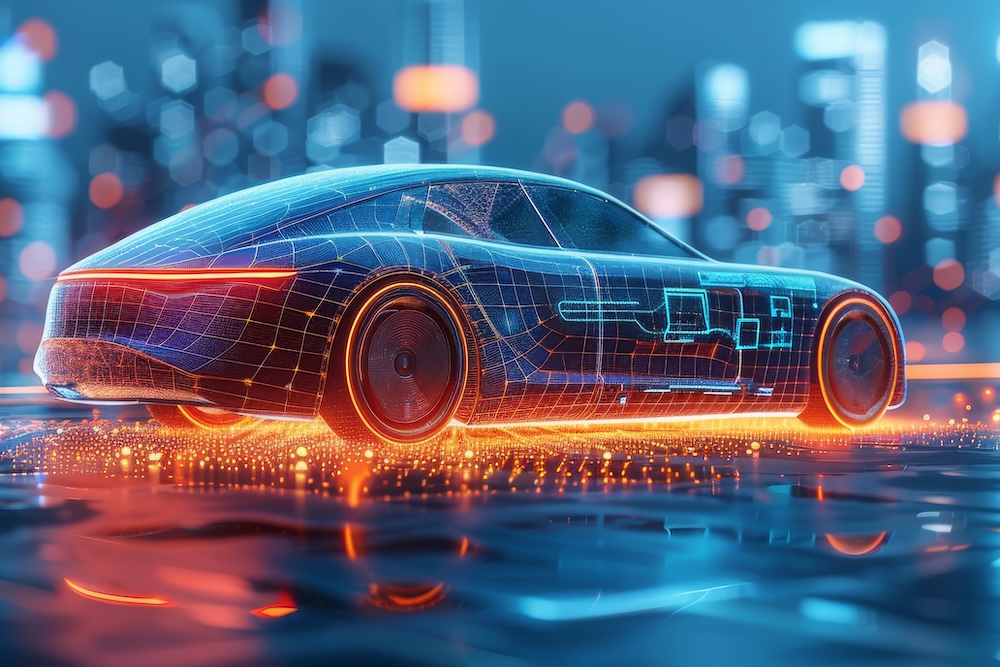
From Chaos to Control: The Future of Automotive E/E Architecture
With Halloween just around the corner, it seemed appropriate to bring a little intrigue and mystery into this week’s blog. In the heart of Silicon Valley is the Winchester Mystery House which, throughout the years, has grown to become a relatively popular tourist attraction.
Owned by Sarah Winchester, the heiress of the Winchester Repeating Arms fortune, (think Winchester rifles), this mansion was constructed over the course of 36 years from 1886 to 1922. The legend goes somewhere along the lines that she regularly heard haunting spirits tell her that tragic things would happen if she ever stopped construction on the house. This was the motivation that caused her to transform her eight-room farmhouse into a 24,000 square foot mansion with 160 rooms, 47 stairways and fireplaces, with 13 baths, 6 kitchens and a host of other amazing factoids regarding the ridiculous size and scale of this mansion.
Beyond its sheer scale, what is most unique about this mansion is that these rooms were added on with very little rhyme or reason or forethought. Sarah Winchester’s obsession with adding rooms led to a floor plan where the location of the rooms and the function that they served were irrelevant. The resulting mansion, that over 12 million people have visited since it was opened to the public in 1923, is a hodgepodge of illogical rooms, hallways, and dead-ends.
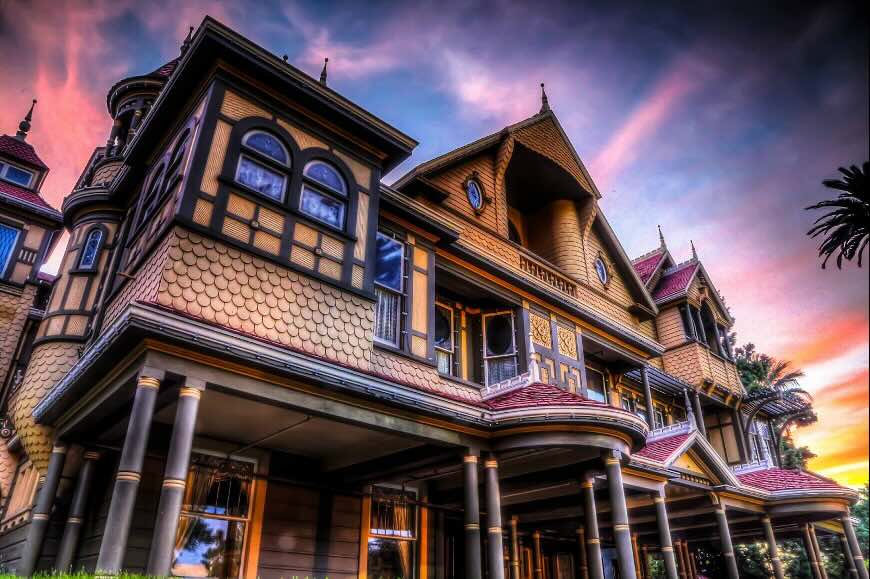
Perhaps a harsh analogy, but in a similar fashion, it feels like throughout the years, the automotive industry has continued to add more and more electronics to the vehicle employing an E/E architecture with similar levels of forethought as Sarah Winchester’s floor plan. The continued addition of electronics has led to high-end vehicles with over 130 microcontrollers that are physically located wherever it seemed to make best sense at the time – resulting in what’s commonly referred to as distributed architecture. The resulting wiring harness required to interconnect all the distributed microcontrollers and other devices, has grown from 55 wires with a total length of 150 ft in 1948 to the present day where the wiring harness for a vehicle based upon a distributed E/E architecture weighs roughly 120 lbs and contains 1,500 to 2,000 wires with a total length of 5,280 feet (one mile).
To a certain degree, it’s not too hard to see how this distributed architecture may have come into existence. More than two decades ago, the automotive OEMs viewed electronics as context, not core to their businesses. This led to the eventual spin-out of the OEMs’ EE teams and the formation of Tier 1s, an external company that had indirect responsibility for the OEM’s electronics and associated E/E architecture.
Today, automotive OEMs are becoming acutely aware of the importance and impact of both the electronics and the underlying E/E architecture. This is driving the mature OEMs to shift back to their original model where the electronics teams were vertically integrated. Fun fact, I have been told that this trend is not uncommon across different industries and that the Harvard Business Review refers to this shift from dis-integration back to vertical integration as “the double helix.”
With this greater, more immediate focus on the electronics and underlying shift to greater control of the vehicle through electronics, there is a similar increase in focus by the OEMs that is placed upon the underlying E/E architecture. More specifically, there is a keen focus on how to reduce the size, weight, complexity, cost, and associated poor reliability of the wiring harness. The impact of the wiring harness, which has typically been considered innocuous, has now become very significant.
EV startups without the baggage of legacy architectures have mostly embraced the centralized E/E architecture, which holds the promise of addressing all the above-mentioned challenges associated with the distributed architecture. However, for most mature automotive OEMs with legacy architectures, the move to centralized can prove too much of a stretch. So the approach is to move from a distributed architecture to a domain architecture and then eventually to the centralized architecture.
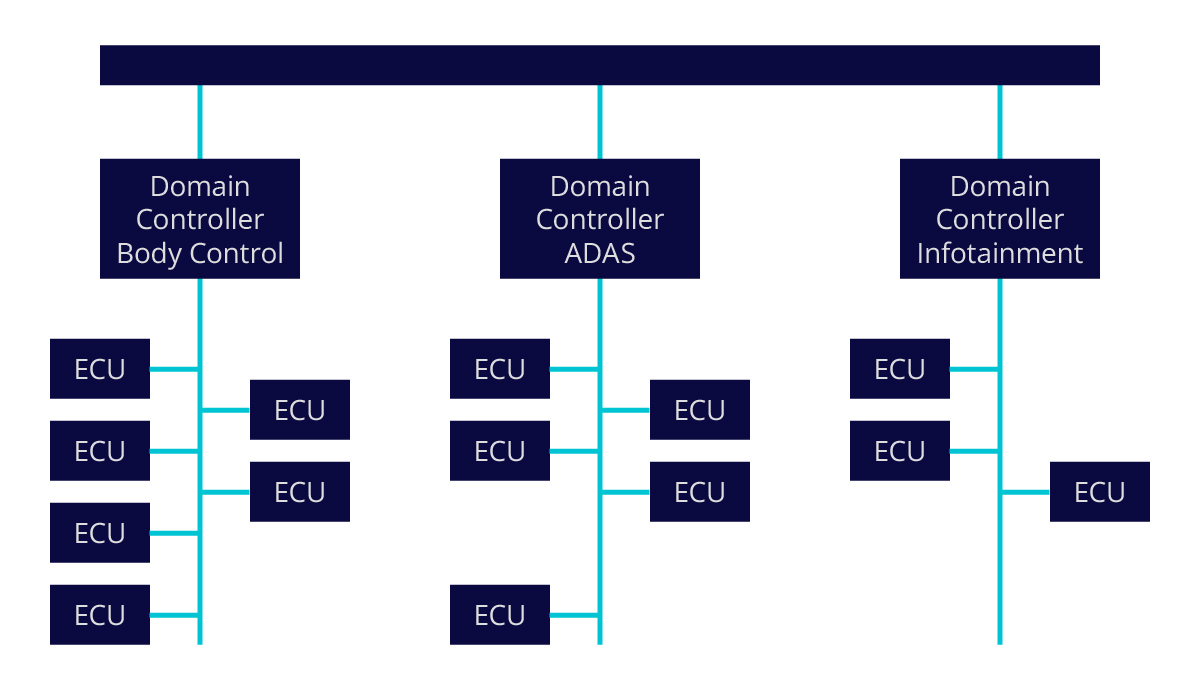
Domain controllers allow for rich communications between electronics control units (ECUs) within a common domain, while isolating unrelated communications between other, unrelated domains.
As shown in Figure 1., one of the key concepts behind the domain architecture is that not all electronics control units (ECUs) need to communicate with one another at all times. This concept is similar to the way that office computer networks are typically constructed. Breaking the network traffic into local area networks with common communication needs leads to greater efficiency and reduced costs. As an example, personnel within an engineering department need to regularly communicate with others in the engineering department, but less frequently with personnel in the shipping department. Breaking these groups into two unique local area networks, i.e. engineering and shipping, allows for rich communication within each group and isolation between the two groups via a bridge. This allows only relevant conversation between either group to occur, and leads to a reduction in wiring while greatly improving communications throughput and reliability.
While the domain architecture offers significant improvements over the distributed architecture, the physical location of the different ECUs directly impacts the physical length of wire required to connect to the appropriate domain controller. The centralized architecture, on the other hand, addresses wiring length and provides many additional, significant benefits.
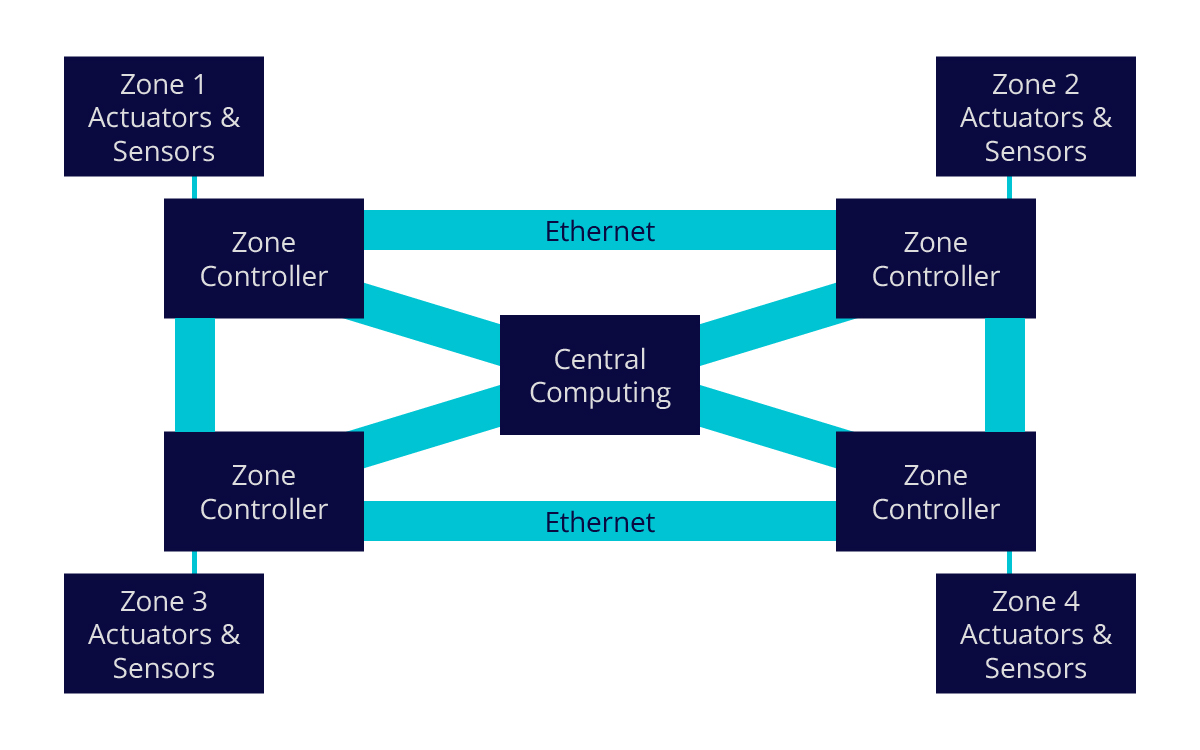
The centralized architecture, as shown in Figure 2, is the eventual, target E/E architecture for most incumbent OEMs. While there are variations on a theme of this actual architecture, typically what they all hold in common is the majority of the computing is aggregated into one common, centralized location. The zone controllers are physically located in different quadrants of the vehicle and connect the different actuators and sensors that are found in the same physical location of a given zone.
For purposes of definition, an example of an actuator would be the physical controller that engages the brakes in the case of anti-lock or automatic emergency braking, whereas a sensor might be a camera or radar that is again, located in the given quadrant, or zone of the vehicle.
As noted in Figure 2., the different zone controllers are interconnected via Ethernet in a mesh configuration – implying that every zone controller has more than one way of connecting to the central computing block. Ethernet connectivity is chosen because it is a very mature, proven, robust serial communication technology that relies on lightweight cabling for connection. Variants of Ethernet, including TSN (time sensitive network) are gaining momentum in automotive as they offer greater levels of determinism in communication timing performance, typically a requirement in real-time embedded applications.
Employing a mesh-based connectivity architecture allows for one or several segments of the network to fail without impact. The network simply seeks an alternative connection path, which is enabled through this scheme. This connectivity topology is typically found in today’s data center in support of what’s referred to as a “fail-over” architecture. As previously mentioned, in many different ways, the vehicle of the future is increasingly becoming a data center on wheels.
The centralization and consolidation of compute resources also leads to a significant reduction in the total number of discrete ECUs while also more readily accommodating computational redundancy, again leading to greater levels of reliability.
Within a given zone, the sensors and actuators can be added based on trim level of the vehicle in a manner similar to populating a PC with a new add-in card. The sensor or actuator identifies its presence and personality to the centralized computer via a unique IP address and the vehicle’s computer’s operation is updated accordingly. This allows for greater levels of simplicity in the manufacturing of different classes of vehicles, which typically contain different numbers and types of sensors and actuators. Different types and numbers of sensors are added on the manufacturing floor based on vehicle type or level. This type of “plug-and-play” also supports the concept of upgrading a vehicle to a higher trim level years after the vehicle has left the showroom floor.
With software scaling into the 100 to 300 millions of lines of code, the importance of practical support of over-the-air OTA software updates cannot be overstated. The distributed architecture with over 130 MCUs that are distributed throughout all corners of the vehicle, does not lend itself to simple OTA updates. A similar point can be made in regards to the manner in which the centralized architecture leads to a more rational and practical way to address cybersecurity.
Without a centralized architecture, the hot industry buzzword, Software Defined Vehicles (SDV) would be almost impossible to realize.
In the same way that the evolving E/E architectures are driving transformation, the SDV is also poised to transform the auto industry in even more significant ways.
This is, however, another topic that I will discuss in a future blog.
With Halloween just around the corner, it seemed appropriate to bring a little intrigue and mystery into this week’s blog. In the heart of Silicon Valley is the Winchester Mystery House which, throughout the years, has grown to become a relatively popular tourist attraction.
Owned by Sarah Winchester, the heiress of the Winchester Repeating Arms fortune, (think Winchester rifles), this mansion was constructed over the course of 36 years from 1886 to 1922. The legend goes somewhere along the lines that she regularly heard haunting spirits tell her that tragic things would happen if she ever stopped construction on the house. This was the motivation that caused her to transform her eight-room farmhouse into a 24,000 square foot mansion with 160 rooms, 47 stairways and fireplaces, with 13 baths, 6 kitchens and a host of other amazing factoids regarding the ridiculous size and scale of this mansion.
Beyond its sheer scale, what is most unique about this mansion is that these rooms were added on with very little rhyme or reason or forethought. Sarah Winchester’s obsession with adding rooms led to a floor plan where the location of the rooms and the function that they served were irrelevant. The resulting mansion, that over 12 million people have visited since it was opened to the public in 1923, is a hodgepodge of illogical rooms, hallways, and dead-ends.
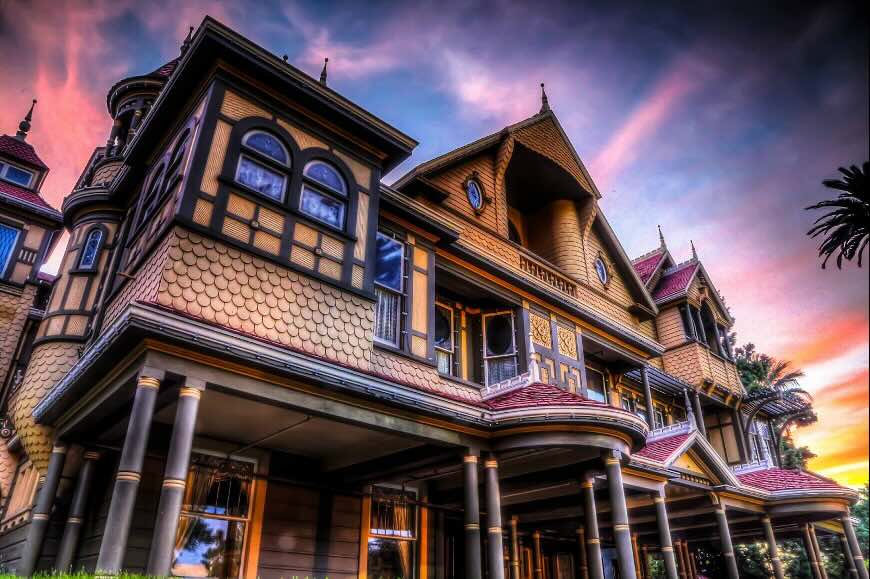
Perhaps a harsh analogy, but in a similar fashion, it feels like throughout the years, the automotive industry has continued to add more and more electronics to the vehicle employing an E/E architecture with similar levels of forethought as Sarah Winchester’s floor plan. The continued addition of electronics has led to high-end vehicles with over 130 microcontrollers that are physically located wherever it seemed to make best sense at the time – resulting in what’s commonly referred to as distributed architecture. The resulting wiring harness required to interconnect all the distributed microcontrollers and other devices, has grown from 55 wires with a total length of 150 ft in 1948 to the present day where the wiring harness for a vehicle based upon a distributed E/E architecture weighs roughly 120 lbs and contains 1,500 to 2,000 wires with a total length of 5,280 feet (one mile).
To a certain degree, it’s not too hard to see how this distributed architecture may have come into existence. More than two decades ago, the automotive OEMs viewed electronics as context, not core to their businesses. This led to the eventual spin-out of the OEMs’ EE teams and the formation of Tier 1s, an external company that had indirect responsibility for the OEM’s electronics and associated E/E architecture.
Today, automotive OEMs are becoming acutely aware of the importance and impact of both the electronics and the underlying E/E architecture. This is driving the mature OEMs to shift back to their original model where the electronics teams were vertically integrated. Fun fact, I have been told that this trend is not uncommon across different industries and that the Harvard Business Review refers to this shift from dis-integration back to vertical integration as “the double helix.”
With this greater, more immediate focus on the electronics and underlying shift to greater control of the vehicle through electronics, there is a similar increase in focus by the OEMs that is placed upon the underlying E/E architecture. More specifically, there is a keen focus on how to reduce the size, weight, complexity, cost, and associated poor reliability of the wiring harness. The impact of the wiring harness, which has typically been considered innocuous, has now become very significant.
EV startups without the baggage of legacy architectures have mostly embraced the centralized E/E architecture, which holds the promise of addressing all the above-mentioned challenges associated with the distributed architecture. However, for most mature automotive OEMs with legacy architectures, the move to centralized can prove too much of a stretch. So the approach is to move from a distributed architecture to a domain architecture and then eventually to the centralized architecture.
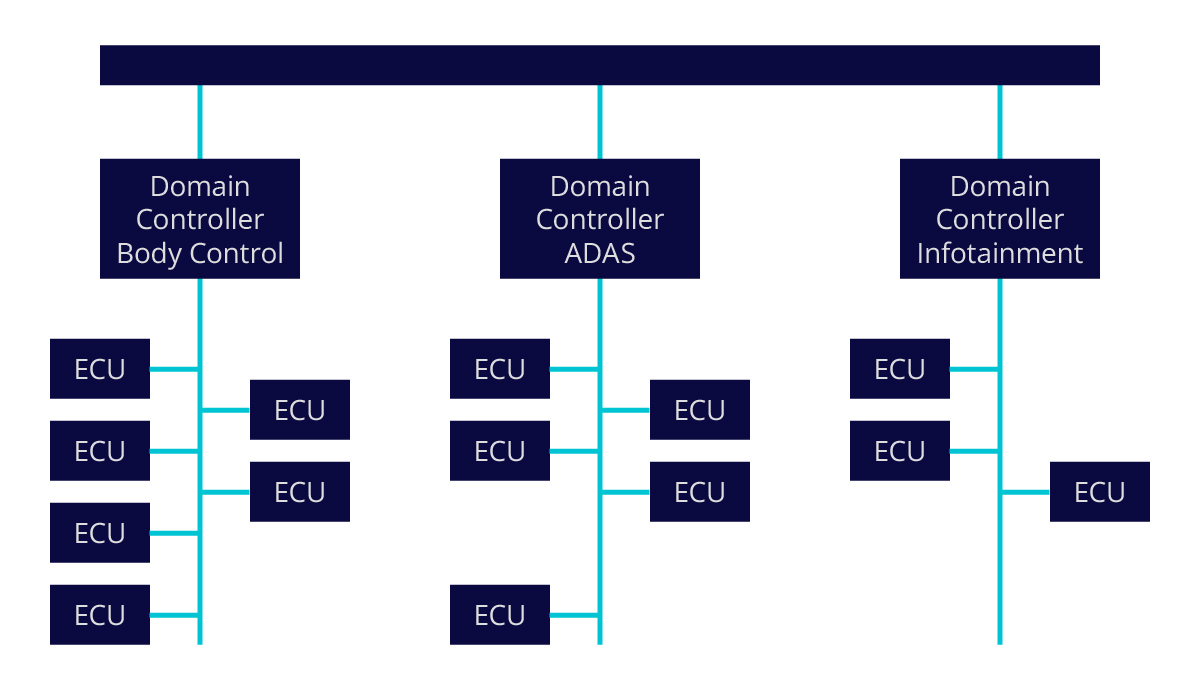
Domain controllers allow for rich communications between electronics control units (ECUs) within a common domain, while isolating unrelated communications between other, unrelated domains.
As shown in Figure 1., one of the key concepts behind the domain architecture is that not all electronics control units (ECUs) need to communicate with one another at all times. This concept is similar to the way that office computer networks are typically constructed. Breaking the network traffic into local area networks with common communication needs leads to greater efficiency and reduced costs. As an example, personnel within an engineering department need to regularly communicate with others in the engineering department, but less frequently with personnel in the shipping department. Breaking these groups into two unique local area networks, i.e. engineering and shipping, allows for rich communication within each group and isolation between the two groups via a bridge. This allows only relevant conversation between either group to occur, and leads to a reduction in wiring while greatly improving communications throughput and reliability.
While the domain architecture offers significant improvements over the distributed architecture, the physical location of the different ECUs directly impacts the physical length of wire required to connect to the appropriate domain controller. The centralized architecture, on the other hand, addresses wiring length and provides many additional, significant benefits.
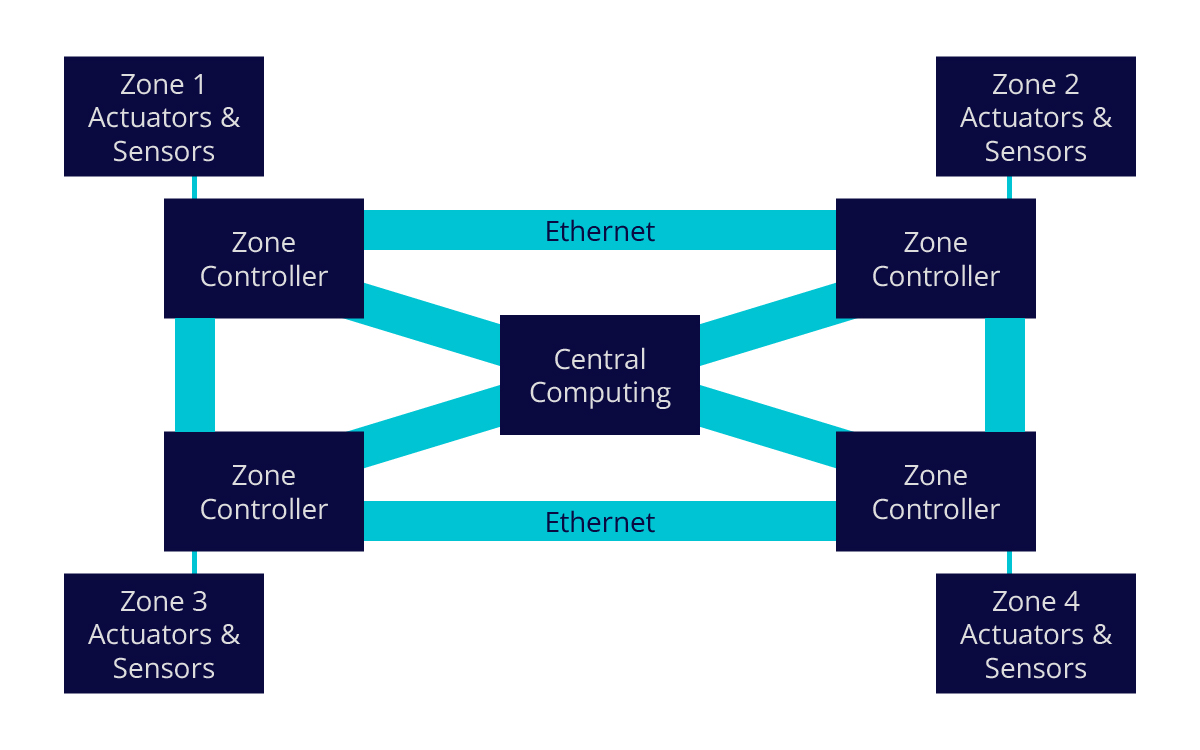
The centralized architecture, as shown in Figure 2, is the eventual, target E/E architecture for most incumbent OEMs. While there are variations on a theme of this actual architecture, typically what they all hold in common is the majority of the computing is aggregated into one common, centralized location. The zone controllers are physically located in different quadrants of the vehicle and connect the different actuators and sensors that are found in the same physical location of a given zone.
For purposes of definition, an example of an actuator would be the physical controller that engages the brakes in the case of anti-lock or automatic emergency braking, whereas a sensor might be a camera or radar that is again, located in the given quadrant, or zone of the vehicle.
As noted in Figure 2., the different zone controllers are interconnected via Ethernet in a mesh configuration – implying that every zone controller has more than one way of connecting to the central computing block. Ethernet connectivity is chosen because it is a very mature, proven, robust serial communication technology that relies on lightweight cabling for connection. Variants of Ethernet, including TSN (time sensitive network) are gaining momentum in automotive as they offer greater levels of determinism in communication timing performance, typically a requirement in real-time embedded applications.
Employing a mesh-based connectivity architecture allows for one or several segments of the network to fail without impact. The network simply seeks an alternative connection path, which is enabled through this scheme. This connectivity topology is typically found in today’s data center in support of what’s referred to as a “fail-over” architecture. As previously mentioned, in many different ways, the vehicle of the future is increasingly becoming a data center on wheels.
The centralization and consolidation of compute resources also leads to a significant reduction in the total number of discrete ECUs while also more readily accommodating computational redundancy, again leading to greater levels of reliability.
Within a given zone, the sensors and actuators can be added based on trim level of the vehicle in a manner similar to populating a PC with a new add-in card. The sensor or actuator identifies its presence and personality to the centralized computer via a unique IP address and the vehicle’s computer’s operation is updated accordingly. This allows for greater levels of simplicity in the manufacturing of different classes of vehicles, which typically contain different numbers and types of sensors and actuators. Different types and numbers of sensors are added on the manufacturing floor based on vehicle type or level. This type of “plug-and-play” also supports the concept of upgrading a vehicle to a higher trim level years after the vehicle has left the showroom floor.
With software scaling into the 100 to 300 millions of lines of code, the importance of practical support of over-the-air OTA software updates cannot be overstated. The distributed architecture with over 130 MCUs that are distributed throughout all corners of the vehicle, does not lend itself to simple OTA updates. A similar point can be made in regards to the manner in which the centralized architecture leads to a more rational and practical way to address cybersecurity.
Without a centralized architecture, the hot industry buzzword, Software Defined Vehicles (SDV) would be almost impossible to realize.
In the same way that the evolving E/E architectures are driving transformation, the SDV is also poised to transform the auto industry in even more significant ways.
This is, however, another topic that I will discuss in a future blog.